Companies are always trying to manage costs, and this is especially true for manufacturers of food products, dietary supplements, pet food, and other regulated products. Many companies turn to in-house lab testing to reduce costs, but many don’t see all the hidden costs and challenges until the project is already underway.
Here, we reveal some of the most important hidden costs of operating an in-house lab and what you need to know to make an informed decision.
1) Laboratory Accreditation: One of the Highest Costs of In-House Lab Testing
Earning accreditation is one of the costliest components of in-house lab testing. Before you say, “Well, we don’t need accreditation,” consider that many top retailers, restaurant chains, and foodservice distributors require you to provide test results from an ISO-accredited laboratory before they will do business with you.
In addition, any reputable food testing laboratory will be accredited. This provides third-party validation of the lab’s quality management system and methodologies.
There are a few major accreditations available, including the following:
- ISO
- USDA
- USDA-AMS Commodity Specific Certifications
The most widespread is ISO 17025, which a lab can earn only after passing a third-party audit from A2LA or another accrediting body.
Preparing for accreditation requires multiple steps that can easily take 9 months or longer and eclipse six figures, depending on your starting point. Here are some of the requirements:
- Proficiency testing to validate the competency of the lab in performing certain methods. This must be done multiple times per year and on an ongoing basis.
- Certification of employee training.
- Internal audits.
- Desk audit every other year.
- Laboratory audit every other year.
- Hiring dedicated personnel or consultants with ISO Expertise.
- Creating multiple required documents & forms and maintaining records.
- Calibration of multiple instruments through a third-party provider.
Passing requires establishing a robust system based on the ISO pyramid. Recordkeeping makes up the foundation, work instructions are built upon that, followed by Standard Operating Procedures (SOPs), your Quality Manual, and finally your policy. Along the way, you need to develop employee training, safety measures, equipment maintenance plans, pest control, and much more.
The financial burden can easily amount to six figures, especially if you hire a consulting firm to help.

2) Liability in Case of a Recall or Adverse Event
Imagine accidentally releasing a product that was contaminated with E. coli or another pathogen that sickened or even killed someone after getting the go-ahead from your in-house lab.
Your company must bear 100% of that responsibility. A recall can costs millions of dollars, in addition to the public relations nightmare that may affect your brand for years.
Outsourcing your testing to a third-party lab helps you bear the burden of liability in the event of a recall, reducing stress for your Quality Control team all the way to the top of the organization. It also reduces the chances of a recall event from happening in the first place since the test results generated would more likely be unequivocal due to the quality system requirements.
3) Can You Find and Retain the Right People for an In-House Lab?
Nearly every company is struggling to hire and retain good people. Finding and retaining qualified personnel for in-house lab testing adds to the burden.
As you may imagine, it’s difficult to find people qualified in microbiology testing and chemistry testing. And given the shortage of qualified people, it’s a challenge to prevent other companies from recruiting them away from your lab.
4) Expensive Equipment and Waste Management
It’s difficult to justify the cost of a test instrument that costs tens of thousands of dollars if you’re only running a few samples per day. A third-party laboratory can spread that cost out to several customers by running dozens of samples a day, helping control costs.
In addition, many companies don’t consider the expense of disposing of hazardous waste when performing a cost benefit analysis of in-house lab testing. Bio-hazardous waste poses a threat to personnel and is expensive to remove. Hiring a sterilization service adds to your costs.
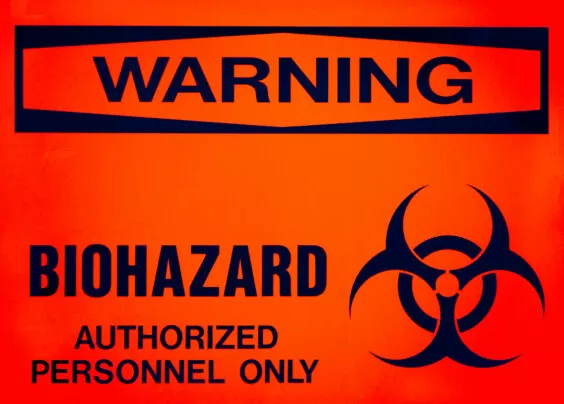
5) In-House Lab Testing Requires Expertise That is Difficult to Find
Petrifilm plates are a cost-effective and relatively simple option that works well for some companies when performing tests for indicator organisms. But pathogen testing is much more complex and often requires precise, sensitive instrumentation (like the Hygiena BAX® SalQuant™ system) that requires expertise to operate properly.
In addition, it takes years to build a body of scientific knowledge that can help guide your team and ensure you’re meeting the highest standards.
One food manufacturer we worked with closed its in-house lab during the Covid pandemic due to staffing issues. It became clear after several conversations that their personnel lacked expertise in important areas.
In fact, switching to our third-party lab for environmental monitoring resulted in more confirmed positives toward which they took more aggressive action, possibly helping prevent contaminated product from reaching commerce.
Their in-house lab testing wasn’t finding these positives due to an outdated methodology being used or requirements that were not being followed. Getting more positives is helping them make a safer product, and now they can focus on what they do best instead of trying to manage an in-house lab.
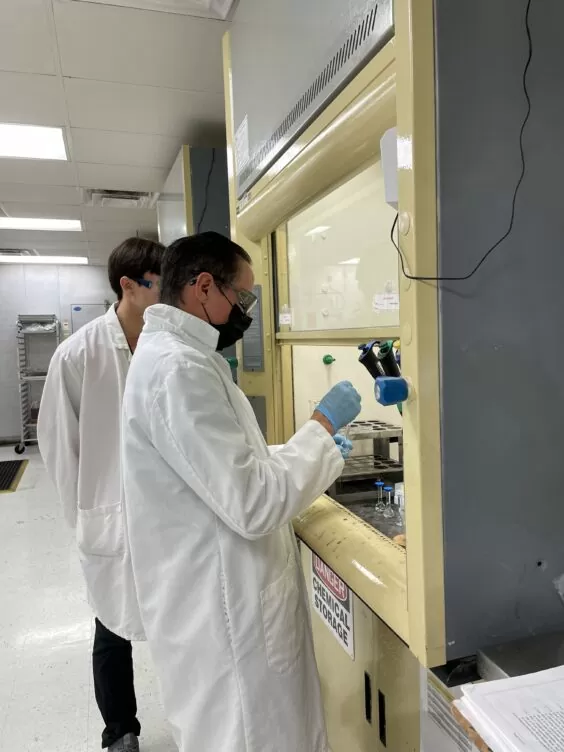
6) Can Your In-House Lab Operate 24/7?
Increasing turnaround time (TAT) is a main reason many companies opt for in-house lab testing. But to leverage the best possible TAT, you need staff working 24/7.
For example, a sample may need to be pulled overnight. In our experience, it’s extremely difficult to get overnight coverage in an in-house lab. It can also be difficult to have technical experts available all the time in case something arises that needs immediate attention.
Improved TAT is a valid reason to pursue in-house lab testing, but consider the staffing requirements of operating 24/7 to reap those benefits.
7) Reduced Buying Power Drives Up the Costs of In-House Lab Testing
Laboratories often face tight supply chains that make it difficult to obtain materials like growth media and lab supplies.
A new in-house lab likely won’t have longstanding relationships with suppliers to leverage when global supplies are short.
In addition, an in-house lab will likely pay 4-5 times more for supplies, unless it has high enough volume to qualify for supplier discounts.
However, a large North American lab will have the influence to obtain supplies during times of constraint. They can also tap into their network for help when needed. For example, Certified Laboratories and Food Safety Net Services (FSNS), both part of Certified Group, maintain 30+ locations across North America, meaning labs can share supplies across the network as needed to meet customer demands, even with tight supply chains.
8) The Value of Third-Party Relationships
Third-party labs often have longstanding relationships with government agencies and trade organizations. These relationships can be beneficial for clients, keeping them informed and helping them navigate challenges. Furthermore, third-party labs are viewed as unbiased parties trusted by regulatory bodies.
Doing your own testing can affect the perception some companies have of your organization. There can be undue pressure for in-house labs to cut corners to provide results faster, or even to retest away positives, leading to inaccurate results and potential public health implications. It can give the impression that the fox is guarding the chicken coop, so to speak.
In-House Lab Testing Often Costs More than it Seems
If you’re thinking of opening an in-house lab for your product testing, it’s essential to consider the hidden costs. Be sure to weigh the costs of accreditation, liability, staffing challenges, equipment, strained supply chains, and reduced buying power in your cost benefit analysis.
We often work with companies that built out their in-house lab only to change tactics down the road due to the high hidden costs. This allows them to focus on manufacturing food products safely, leaving the technical expertise to us.